Whether it's a hybrid electric vehicle (HEV), a plug-in hybrid electric vehicle (PHEV), or a battery electric vehicle (BEV), the traction inverter, as a key component of the electrified powertrain, affects the driving experience, battery endurance, and overall vehicle safety.
The traction inverter is located between the high-voltage system battery and the electric motor. It converts the high-voltage DC voltage into three AC outputs to drive the motor. The traction inverter integrates many technologies to handle torque commands from the vehicle control unit (VCU) and to safely control the motor as needed. The vehicle's range is directly related to the efficiency of the traction inverter and the motor throughout the driving process, including acceleration, steady state, and energy recovery to the battery through regenerative braking.
The traction inverter mainly consists of a four-quadrant chopper, an intermediate voltage circuit, a braking chopper, and a pulse-width modulation inverter. The four-quadrant chopper is used to convert DC power to AC power, and to achieve energy conversion and control during the conversion process; the intermediate voltage circuit is used to stabilize the output voltage to ensure the normal operation of the traction motor; the braking chopper is used to convert the reverse electrical energy generated during the braking process into electrical energy and store it to improve the efficiency of energy utilization; the pulse-width modulation inverter is used to control the frequency and waveform of the output current to achieve start, braking, and speed control of the AC traction motor.
Advertisement
There is at least one traction inverter on an electric vehicle, and some models have two, one on the front axle and one on the rear axle. In some high-end vehicles, each wheel has a traction inverter.
From the technical development trend of inverter and motor control, the power level is continuously increasing. Currently, the power level of mainstream cars is about 60~80 kilowatts, and the power level of the next generation of electric vehicles ranges from 100 kilowatts to 500 kilowatts, or even more. In addition, a higher battery voltage is also a development trend, from 400V to 800V, and higher system integration, power density, and efficiency are also development trends.
01
IGBT and SiC, GaN power switchesThe power switch is a core component in the traction inverter, and the Insulated Gate Bipolar Transistor (IGBT) is commonly used. However, wide-bandgap (WBG) power switches, such as Silicon Carbide (SiC) and Gallium Nitride (GaN), can provide significant advantages, including higher switching rates, leading to higher efficiency and power density, as well as smaller supporting components to reduce the size of the motor.
Since Tesla announced in 2021 that the Model 3 is equipped with SiC power devices, SiC has embarked on a rapid deployment path, and this field has become increasingly lively. At present, among overseas car companies, in addition to Tesla using SiC devices in the traction inverter, Toyota's bZ4X, Mirai, Prius, and Lexus RZ have also started to adopt SiC devices. In addition, Honda, Ford, Volkswagen, and other manufacturers have also begun to adopt SiC solutions.
Among Chinese car companies, BYD has made significant technical breakthroughs in SiC, and flagship models such as BYD Han and Tang 4WD have extensively used SiC modules. NIO's ET7, ES7, ES8, and EC7 models have also used SiC electric drive systems, and XPeng G9 has adopted SiC devices. Ideal has also started to plan SiC solutions, and its power semiconductor research and development and production base was established in Suzhou in May 2023, focusing on the research and development and production of SiC automotive-grade chip modules, which is expected to be officially put into production in 2024. In addition, Dongfeng and Geely have also carried out relevant layouts.
For SiC devices to further popularize, the following challenges need to be addressed: the challenges brought by high switching speeds, the extremely high switching speed has brought challenges to the design of the driving circuit, requiring the design of fast and accurate driving circuits to ensure that SiC devices can accurately perform the required switching operations; the high-temperature working environment has put forward higher requirements for the driving circuit, requiring the design of driving circuits that can withstand high temperatures and ensure their stability and reliability under high-temperature conditions; due to the high-speed switching characteristics of SiC devices, electromagnetic interference is easily generated, affecting the surrounding electronic equipment and systems, therefore, effective electromagnetic interference suppression measures need to be taken in the design of the driving circuit; SiC devices have characteristics such as fast switching frequency and short circuit time, which put forward higher requirements for protection technology; the manufacturing cost of SiC devices is relatively high, which limits its use in some applications, and performance and cost factors need to be considered comprehensively in the design of the driving circuit to achieve the best cost-effectiveness.
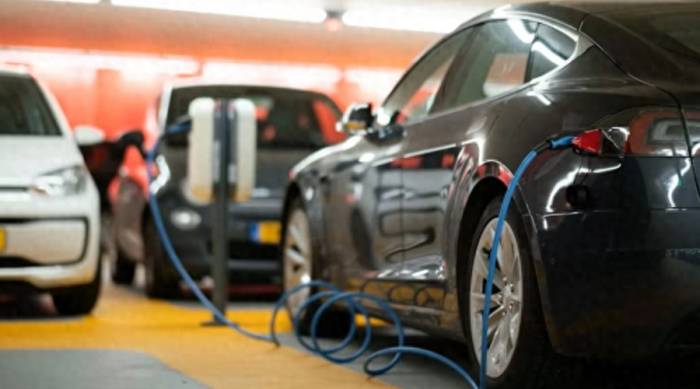
To address the above challenges, continuous technical research and innovation are needed to improve the performance and reliability of the driving circuit.
In addition to SiC, GaN has also begun to be applied in electric vehicles, especially in 400V and 800V electric vehicle traction inverters. Compared with SiC power devices, the advantages of GaN are still obvious.
GaN power devices can greatly improve energy efficiency, reduce energy loss by nearly 40%, and increase power density by 33%, achieving a more compact and lightweight traction inverter design. Overall, a 400V traction inverter based on GaN design can meet the market's demand for electric vehicles with more affordable prices and higher endurance capabilities.
The application of traction inverters based on GaN three-stage topological design in 800V systems is accelerating, and its advantages mainly include: the three-stage GaN topological design not only reduces switching loss and improves efficiency but also reduces high-frequency copper loss and iron loss in filters and motors, and the overall efficiency is greatly improved compared with the two-stage topological design system; reduced noise, vibration, and electromagnetic interference; optimized durability and reliability, and the circuit operation is smoother and more stable. In addition, the three-stage GaN topology can reduce the load on the motor bearing, and the improved durability and reliability help extend the overall system service life.
For example, the All-GaN Car jointly developed by Toyota and Nagoya University uses GaN power devices in the traction inverter, on-board charger, and DC-DC converter. Compared with the conventional IGBT solution, GaN not only improves power density but also increases efficiency by 20%, extending the vehicle's driving range.
The well-known engineering company Ricardo designed and compared a 30kW GaN inverter with a SiC inverter, and the test results showed that GaN reduced power loss by 25% and increased power density by 33% compared to the SiC solution. Many Tier 1 and OEM car manufacturers have also obtained similar results in the design of 250kW traction inverters.Global Electric Vehicle Traction Inverter Market Landscape
According to TrendForce statistics, influenced by the traditional off-season for electric vehicles, the global installation volume of traction inverters in the first quarter of 2024 was 5.22 million sets, a decrease of 27% compared to 7.14 million sets in the fourth quarter of 2023. Among them, the installation volume of traction inverters for pure electric vehicles accounted for 48%, a decrease of 5% quarter-on-quarter, while the installation volume of traction inverters for hybrid and plug-in hybrid electric vehicles increased from 47% to 52%.
Looking at the installation volume of traction inverters in various voltage ranges for electric vehicles in the first quarter, due to the growth of hybrid models, the installation volume of traction inverters with a voltage ≤300V accounted for 36%, an increase of 2% quarter-on-quarter; the decline of pure electric vehicles led to a decrease of 1% in the installation volume share of the 300V-550V voltage range, down to 55%, and the installation volume share of >550V remained at 9%, consistent with the previous quarter. Although there were slight fluctuations in the proportion of each range, the mainstream voltage range in the market is still 300V-550V.
Globally, the main manufacturers of electric vehicle traction inverters include Denso (Electric Equipment), Delta Electronics, Bosch, Tesla, Mitsubishi Electric, DANA TM4, Voith Turbo, Hitachi, Continental, Toshiba, Valeo, and BYD, HuiChuan Technology, and Huawei, among others.
Let's take Denso and Tesla, which are among the top three globally, as examples to introduce the technology and product capabilities of top-tier traction inverter manufacturers.
Denso places great emphasis on SiC devices and has developed an SiC boost power module. Compared to the traditional silicon IGBT power module, its volume has been reduced by 30%, and power consumption has been reduced by 70%. The reduction in power consumption has reduced the volume of the boost power module and improved the vehicle's fuel efficiency.
Toyota launched the Mirai model in December 2020, which uses this module composed of SiC diodes and transistors. As early as 2018, Toyota used Denso's SiC diodes in its Sora fuel cell bus.
The relationship between Denso's SiC devices and Toyota can be traced back to the 1980s when the two companies joined hands to conduct basic research on this wide-bandgap semiconductor material. It was not until 2007 that Toyota and Denso officially announced the joint development of SiC devices and their application in practical use.
In 2014, they achieved their first breakthrough when Toyota announced the use of SiC devices in the power control unit (PCU) of the Prius. The Prius is a hybrid electric vehicle launched by Toyota in 1997. The PCU is responsible for controlling the motor drive power in hybrid electric vehicles and other vehicles with electric systems, and it consumes about a quarter of the total power consumption of the vehicle.According to tests, the PCU using SiC devices has improved the fuel efficiency of the Prius by 10%. Toyota will test these SiC-based PCUs in the Camry hybrid prototype to examine how the internal boost converter and inverter of the PCU can improve voltage, current, and thermal management performance.
In addition, Denso has also adopted Showa Denko's SiC epitaxial wafers for its power control module, and the company has already applied these modules in its onboard battery chargers and fast charging stations for electric vehicles.
The inverter system of the Tesla Model 3 is renowned for its innovative design.
The Model 3 is the first model to integrate a full SiC power module, and Tesla's inverter consists of 24 1-in-1 power modules, which are mounted on a pin-fin heatsink. The SiC MOSFETs used are designed and manufactured using STMicroelectronics' technology, enabling them to reduce conduction losses and switching losses. This is concluded from a comprehensive teardown analysis of the Model 3, which also provides an estimate of the production cost of SiC MOSFETs and their packaging. In this technology, the design of the pin-fin heatsink is crucial for improving heat dissipation efficiency. The pin-fin design increases the surface area, thereby improving heat transfer efficiency, which is very important for managing the heat generated by the SiC MOSFET during high-efficiency operation.
Through cooperation with STMicroelectronics, Tesla has been able to use the latest technology to manufacture SiC MOSFETs, which not only enhances the performance of electric vehicles but also helps to reduce production costs, further promoting the application of SiC technology in the field of electric vehicles.
The core of the Model 3 inverter is the power module, which is composed of high-efficiency semiconductor devices responsible for the conversion of electrical energy. SiC devices significantly improve the efficiency of the inverter with their lower power loss, higher switching frequency, and better thermal performance, achieving a more compact design.
The control circuit of the Model 3 inverter is responsible for fine-tuning the power conversion process. It precisely monitors the motor speed and torque requirements to ensure seamless integration with various driving modes of the vehicle. Tesla's control algorithms can accurately control the switching mode of the inverter, optimize power output, and enhance the overall driving experience.
Overall, the key features and technological innovations of the Model 3 inverter are mainly reflected in the following aspects: SiC MOSFET technology; quasi-modular design, combining the advantages of traditional modular design and discrete components, with the inverter composed of 24 units integrated with power modules, each module having a high individual power level; high integration, reducing the number of components and external connections, simplifying system complexity, and improving reliability; cost-effectiveness, although the cost of SiC MOSFETs is high, cost-effectiveness can be achieved by reducing the number of components and optimizing the design; the inverter adopts an effective thermal management scheme, including a substrate with high thermal conductivity and advanced cooling design, to ensure stability under high-power working conditions; innovative packaging, Tesla cooperated with STMicroelectronics to develop a new packaging solution, combining the low cost of plastic packaging and the electrical isolation of modular packaging; the inverter design considers the close integration of software and hardware to achieve better system control and performance optimization.
03
The rise of Chinese manufacturersThe introduction above pertains to international giants who have been deeply involved in the inverter domain for many years. With their profound technological accumulation and market influence, they have consistently occupied a significant market share. However, due to the rapid rise of China's electric vehicle manufacturing and consumer market, it has spurred the rapid catch-up of domestic related parts technology and products, prompting the industry status of related manufacturers to improve considerably within a relatively short period of time.
According to TrendForce statistics, among the top five global traction inverter Tier 1 suppliers, there are already two Chinese companies: BYD and Inovance Technology. Among them, BYD's inverters are self-developed and self-produced products used for their own vehicle models, while Inovance Technology is deeply involved with innovative new energy vehicle companies such as Li Auto, XPeng, and Xiaomi. In addition, Huawei's market share has increased by 1% for three consecutive quarters, and it is worth watching whether it can enter the top five suppliers in the future. In the first quarter of 2024, the market share of Chinese companies, including BYD and Inovance Technology, reached 34%, breaking the situation where the traction inverter market was dominated by European, American, and Japanese Tier 1 suppliers.