As the global acceptance of electric vehicles continues to grow, silicon carbide (SiC) is poised to seize a new growth opportunity in the next decade. It is anticipated that manufacturers of power semiconductors and players in the automotive industry will become more actively involved in the construction of the value chain in this field.
SiC, as a third-generation semiconductor, has once again set off a trend this year with its superior performance.
01
Transition from 6-inch to 8-inch drives
Due to the lack of mass shipment in the open SiC wafer market by 2024, the 8-inch SiC platform is considered to be of strategic significance.
SiC has characteristics such as high breakdown field, high saturated electron velocity, high thermal conductivity, high electron density, and high mobility, making it an excellent semiconductor material. It has already been widely applied in fields such as automotive electronics and industrial semiconductors. After entering the 8-inch phase, the theoretical number of available bare chips (die) per wafer will significantly increase. According to data from Wolfspeed's financial report, in terms of wafer processing costs alone, although the wafer cost increases when upgrading from 6-inch to 8-inch, the number of good bare chips (die) obtained from an 8-inch wafer can increase by 20% to 30%, resulting in higher output and ultimately lower chip costs.
Advertisement
Therefore, large-size substrates are gradually being expected due to their cost advantages.
According to calculations by TankeBlue Semiconductor, a Chinese SiC substrate manufacturer, the cost per piece is expected to be reduced by 50% when upgrading from 4-inch to 6-inch; and it is expected that the cost can be further reduced by 35% from 6-inch to 8-inch.At the same time, 8-inch substrates can produce more chips, thereby reducing edge waste. In simple terms, the utilization rate of 8-inch substrates is higher, which is also the main reason why major manufacturers are actively developing.
At present, 6-inch SiC substrates still dominate the market, but 8-inch substrates have begun to penetrate the market. For example, in July 2023, Wolfspeed announced that its 8-inch wafer factory has begun to ship SiC MOSFETs to Chinese customers, indicating that its 8-inch SiC substrates have been shipped in batches. TankeBlue Semiconductor has also begun to ship 8-inch substrates in small quantities, and plans to achieve medium-scale shipments by 2024.
Since Wolfspeed first demonstrated samples in 2015, 8-inch SiC substrates have gone through a development history of 7-8 years, and the technology and product development have accelerated significantly in the past two years. Looking at international manufacturers, in addition to Wolfspeed, which has achieved mass production, there are 7 SiC substrates and epitaxial manufacturers that are expected to achieve mass production of 8-inch substrates this year or in the next 1-2 years.
In terms of investment, Wolfspeed continues to build the John Palmour Silicon Carbide Manufacturing Center (SiC substrate factory) in North Carolina, USA. This factory will further drive the expansion of substrate production capacity to meet the growing demand for 8-inch wafers.
Coherent Company also announced plans last year to expand the production of 8-inch substrates and epitaxial wafers, with large-scale expansion projects in the United States and Sweden. In terms of product export channels, Coherent has received a $1 billion investment from Mitsubishi Electric and Denso, to provide the two companies with 6/8-inch SiC substrates and epitaxial wafers for the long term.
STMicroelectronics also invested in the 8-inch field last year, in cooperation with Hunan San'an Semiconductor to build an 8-inch SiC wafer factory. The latter will build an 8-inch SiC substrate factory to ensure a stable supply of materials for the joint venture. At the same time, ST is developing its own substrates, and has achieved mass production of 8-inch SiC substrates in cooperation with Soitec.
In terms of domestic manufacturers, more than 10 companies have entered the sample and small-scale production stage of 8-inch SiC substrates. These include Semisic Crystal Co., Jing Sheng Mechanical and Electrical, SICC Co., Summit Crystal Semiconductor Co., Synlight Semiconductor Co., TanKeBlue Semiconductor Co., Harbin KY Semiconductor, IV Semitec, Sanan Semiconductor, Hypersics, and other companies.
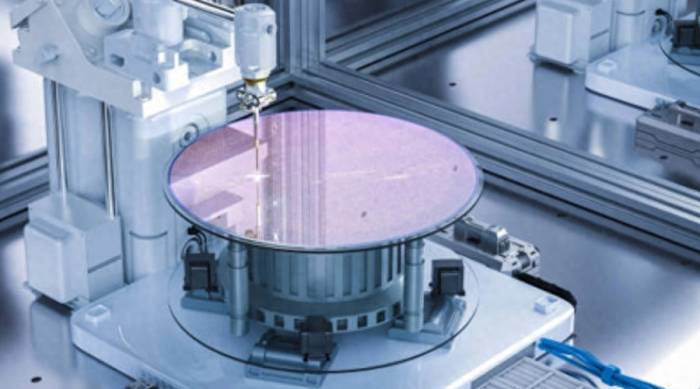
At present, the gap between Chinese substrate manufacturers and international giants has been significantly narrowed. Companies such as Infineon have established long-term partnerships with Chinese manufacturers such as SMIC and Tangke Lan Semiconductor. From a technical perspective, this narrowing of the gap reflects the overall progress of global substrate technology. Looking forward, it is expected that the joint efforts of various manufacturers will promote the development of 8-inch substrate technology.Overall, the overall development momentum of 8-inch SiC substrates is strong.
02
Global 8-inch SiC factories are accelerating expansion
With the continuous breakthrough of substrate materials in technological ceilings, the scale of global 8-inch SiC wafer factory expansion in 2023 has reached a new high.
According to TrendForce statistics, there are about 12 expansion projects related to 8-inch wafers in 2023, of which 8 projects are led by global manufacturers such as Wolfspeed, Onsemi, STMicroelectronics, Infineon, and Rohm. STMicroelectronics also cooperated with San'an Semiconductor on a project. In addition, there are 3 projects led by Chinese manufacturers such as Global Power Technology, Lianxing Technology, and J2 Semiconductor. From a regional perspective, it is expected that key regions such as Europe, the Americas, Japan, South Korea, China, and Southeast Asia will invest heavily in the construction of new 8-inch SiC wafer factories. Up to now, there are about 11 8-inch wafer factories under construction or planning worldwide.
Looking at the expansion direction of manufacturers, Bosch and ON Semiconductor's investments in 2023 are directly aimed at the automotive SiC market. STMicroelectronics also plans to build an 8-inch SiC chip factory in Italy targeting the electric vehicle market. Although other manufacturers have not yet clearly defined the future direction of production capacity, electric vehicles are the main growth engine for SiC both currently and in the future, becoming the focus of major manufacturers' expansion.
From a cost perspective, although 6-inch wafers are the mainstream in the short term, the trend towards larger sizes such as 8-inch to reduce costs and improve efficiency is inevitable. Therefore, it is expected that the electric vehicle market will continue to drive the demand for 8-inch wafers in the future.
From the perspective of the supply chain, the transition to 8-inch wafers is a breakthrough for SiC manufacturers. According to industry insights, the 6-inch SiC device market has entered a stage of fierce competition, especially SiC JBD. For smaller and less competitive enterprises, profit margins are increasingly squeezed, indicating that a new round of integration and restructuring is coming in the future.
The development history of silicon-based semiconductors has proven that using larger wafers can improve productivity. This is one of the main reasons why more and more manufacturers are actively promoting 8-inch wafers.Capital's Advance
It is reported that at the recent financial performance conference held by Rohm, the company's president, Isao Matsumoto, announced that business negotiations with Toshiba in the semiconductor business will begin in June of this year, and it is expected that the negotiations will last for about a year. The two companies aim to strengthen all aspects of cooperation in their semiconductor businesses, covering areas such as technology development, production, sales, procurement, and logistics.
Matsumoto stated: "Toshiba and our semiconductor businesses are very balanced and highly compatible in all aspects, including product portfolios. We hope to make suggestions on how to create this synergy." The two parties envision reducing costs by bulk purchasing common equipment and components, selling internal equipment to each other, and outsourcing product sales to each other.
Previously, Rohm and Toshiba announced that they would cooperate in the production of silicon carbide (SiC) and silicon (Si) power semiconductor devices, a plan that has also been supported by the Japanese government. The plan aims to allow Rohm and Toshiba to focus on SiC and Si power semiconductors respectively, complement each other based on each other's production advantages, and effectively improve supply capacity. The total investment of the project is 388.3 billion yen (equivalent to about 18 billion yuan), of which the government will support 129.4 billion yen (equivalent to about 6 billion yuan), accounting for as much as one-third. The factory of Rohm located in Miyazaki Prefecture will be responsible for producing SiC power devices and SiC wafers, while the factory of Toshiba located in Ishikawa Prefecture will mainly produce Si chips.
In addition, Rohm plans to invest 510 billion yen in the SiC business as a whole before the fiscal year 2027 (equivalent to about 23.7 billion yuan). By the fiscal year 2027, Rohm expects the sales of SiC power devices to increase to 270 billion yen (equivalent to about 12.5 billion yuan), which is 9 times that of the fiscal year 2022. Toshiba's responsibility for the traditional Si semiconductor business will enable Rohm to focus its investment on more cutting-edge SiC products.
Due to the optimistic view that demand from electric vehicles (EV) will expand, Toshiba, Rohm, and other Japanese manufacturers have begun to increase production of next-generation semiconductors that enhance energy-saving performance for EVs. The targets of the increased production of Japanese manufacturers are power semiconductor products used to supply and control electrical power, but the materials used are not the current mainstream silicon (Si), but SiC. If SiC power semiconductors are used on EV inverters, power consumption can be reduced by 5-8%, and the driving range can be increased. Currently, Tesla and some Chinese car manufacturers have begun to use SiC power semiconductors in some models.
Due to the optimistic view that demand from EVs is expected to expand rapidly, Toshiba's semiconductor business subsidiary "Toshiba Electronic Devices & Storage" plans to increase the production of SiC power semiconductors at its Himeji semiconductor factory to three times that of the 2020 fiscal year in the 2023 fiscal year, and then plans to further increase it to ten times by the 2025 fiscal year, with the goal of obtaining more than 10% of the global market share by the 2030 fiscal year at the latest.
In addition, Rohm will invest 50 billion yen, aiming to increase the production capacity of SiC power semiconductors to more than five times the current level by 2025. The new SiC factory of Rohm, located in Chikuho City, Fukuoka Prefecture, has been completed, with the goal of starting operation in 2022. Geely Automobile's EV has decided to adopt Rohm's SiC power semiconductor products, and Rohm aims to increase the global market share from the current nearly 20% to 30% in the early stage.Rohm has always been at the forefront in this field, mass-producing the world's first SiC transistor in 2010. The acquisition of the German subsidiary SiCrystal in 2009, which manufactures SiC wafers, has endowed Rohm with the capability to produce from start to finish. It recently opened an additional production facility at a factory in Fukuoka Prefecture, Japan, as part of a plan to increase production capacity by more than five times.
Fuji Electric is considering advancing the start of SiC power semiconductor production from the original plan (2025) by half a year to one year.
A survey report published by Fuji Keizai, a Japanese research institution, points out that in the long run, with the decline in vehicle prices and the improvement of infrastructure, EVs will become the mainstream of electrified vehicle models. It is estimated that the global EV sales volume in 2035 will increase significantly to 24.18 million units, which is a 10-fold increase (approximately 1,000% growth) compared to 2020.
The survey report published by Fuji Keizai indicates that after 2021, driven by demand from the automotive and electronic device sectors, it is estimated that the next-generation power semiconductor market, including SiC and gallium nitride (GaN), will grow at an annual rate of nearly 20%. The market size is expected to reach 24.9 billion yen by 2030, which is a 3.8-fold increase (about 380% growth) compared to 2020.
Among them, due to the demand from the automotive and electronic device sectors, the demand from China, North America, and Europe is rising. It is estimated that the market size of SiC power semiconductors will expand to 18.59 billion yen by 2030, which is a 2.8-fold increase compared to 2020; the market size of GaN power semiconductors is expected to expand to 1.66 billion yen, which is a 6.5-fold increase compared to 2020; the market size of gallium oxide power semiconductors is estimated to be 4.65 billion yen.