TSMC's lead in advanced manufacturing processes remains evident.
UBS holds the Asian Investment Forum, with Chief Global Equity Strategist Andrew Garthwaite optimistic about generative AI technology increasing productivity by at least 1% annually starting from 2028, and he also has a positive outlook on TSMC and Samsung.
The Hong Kong Economic Times reports that the UBS Asian Investment Forum took place in Hong Kong, discussing global economic trends and stock market development. On the hottest topic of AI, Andrew Garthwaite said that generative AI technology is light on capital, and currently, 20% of personal computers are open to support, with an unprecedented coverage rate. It is estimated that starting from 2028, generative AI technology can increase productivity by at least 1% per year.
Under these circumstances, Andrew Garthwaite believes that the stock market is slightly undervalued, with about 6% growth potential. From a long-term strategy perspective, TSMC is the most attractive investment choice, while the best short-term choice is Samsung.
Andrew Garthwaite analyzes TSMC's advantages, including a 5-year lead in technology over mainland Chinese peers and a 2-year lead over American peers. It almost controls the production of all advanced process chips, and the advantage of being the world's largest wafer foundry system is hard to surpass.
Advertisement
Opinions in the market vary. According to the Central Broadcasting Network, Yang Ruilin, the research director of the Industrial Technology Research Institute's International Research Institute, pointed out that TSMC's latest technological vision, through complementary metal-oxide-semiconductor field-effect transistors, aims to integrate over 200 billion transistors on a single chip at 1.6nm or even below 1nm processes, and even integrate over 1 trillion transistors through 3D packaging, establishing TSMC's leading position at least until 2030.The following article has been translated into English:
Western Countries Can't Do These Things: TSMC Veteran Reveals Key Advantages in Chip Manufacturing
The progress difference between TSMC's factories in Kumamoto, Japan, and Arizona, USA, has always been a hot topic of discussion. Yang Guanglei, who once served as the head of R&D at TSMC, pointed out that the "Confucian culture" in Asia can perfectly fit modern chip manufacturing based on his decades of observation in the chip industry.
"The most difficult part of semiconductor manufacturing is that it has more than 1,500 production steps, each of which requires highly accurate measurement, human wisdom, and experience and knowledge to be well done," said Yang Guanglei, who is currently a visiting professor at the National Taiwan University's Key Technology Research Institute. "For any country that wants to develop its own semiconductor supply chain, talent is the most critical factor."
Yang Guanglei pointed out in an interview that well-trained engineers and disciplined work culture are the two major advantages for Asia to produce advanced semiconductors, and these advantages should not be taken for granted.
Because chip manufacturing involves a complex process, most of the time, it must be executed by highly accurate and well-trained people, while also being able to strictly follow rules and standard operating procedures to make good chips, "not suitable for too much debate."
Considering these factors, Yang Guanglei believes that the work culture in China and South Korea is most suitable for the development of semiconductor manufacturing, "requiring a group of professionals with solid engineering training, and they are willing to follow orders and work overtime to do things well." Yang Guanglei said that Japan also has a similar work culture, which is conducive to the country's reconstruction of its chip industry.
The report points out that Confucian culture emphasizes respect for elders and experienced mentors, as well as maintaining traditions, and also focuses on social harmony and collectivism, where the welfare of the group is more important than individual interests.
In contrast, Western cultural values prioritize creativity, innovation, and independent thinking. The United States and Europe gave up their initial leading position in the semiconductor field to Asian countries decades ago. Yang Guanglei said that if the United States wants to regain the advantage in chip manufacturing, it must embrace Asian culture to some extent, as in the 1980s, and accept immigrants with professional technology.
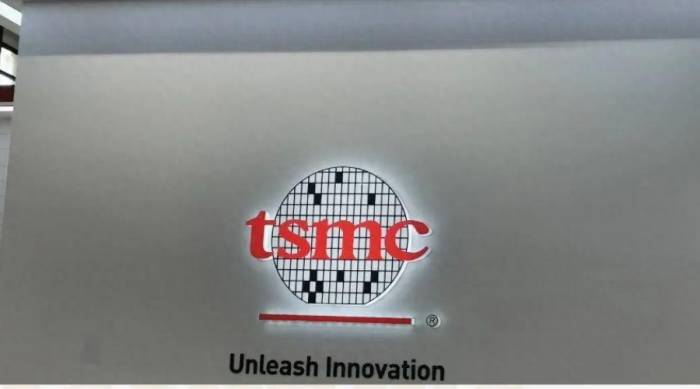
At present, the United States is actively attracting TSMC to manufacture in the United States, offering a cash subsidy of 6.6 billion US dollars and a low-interest loan of 5 billion US dollars, allowing TSMC to build three wafer factories in Arizona.
However, the cultural conflict between the East and the West makes it difficult for TSMC to build factories in the United States. The huge contrast in work culture has created a gap, with American employees not understanding TSMC's strict hierarchy and long working hours, while headquarters employees feel that American colleagues earn more and leave work early.Dozens of new American employees have resigned before their training was completed, and one former employee even bluntly stated that TSMC is the worst employer on the planet.
TSMC founder Zhang Zhongmou once said that if the equipment at the American factory breaks down at 1 a.m., engineers will wait until 8 a.m. the next day to repair it; but if it happens at TSMC's headquarters, engineers will rush back to the factory immediately after receiving a phone call in the middle of the night.
Currently, on the American workplace rating website Glassdoor, TSMC's rating is only 3.2 stars (out of 5), while Intel and Texas Instruments, which are also American chip manufacturers, both have ratings of 4.1 stars.
At the beginning of this month, TSMC promised to build a third advanced chip factory in the United States. However, the progress of TSMC's first phase factory in Arizona is still seriously behind schedule, and the mass production time has been postponed to 2025.
In contrast, the Kumamoto factory in Japan, which started construction a year later than the aforementioned factory, has already started production in February this year.